I hope you're not fed up with newsposts yet... but that will be the last one during my Greek-visit 
Okay, before we start, one more video of the current CNC Milling:
First you can see the final step of the tooling for the keyboard part. The copper slowly cuts into the metal using electricity.
That takes quite a while.
The second thing you can see is basically the LCD frame being "stamped" into the metal... you can imagine how long that takes.
It's a slow process, but the only way to do it accurately without any issues.
The last thing you can see is a typical CNC drill that mills into the metal block. That ALSO takes a while, as you can it is moving slowly.
Yes, creating molds suitable for plastic injection is a quite a lengthy job, if done right.
Altogether, the Pyra will have 7 molds.
Here are some more pictures of the same process. Sorry for the quality, I only had my mobile phone with me today
Okay, let's talk about the colors now!
So, the material we're using for the Pyra is the transparent one you've seen in the video yesterday... nearly unbreakable Polycarbonate.
How does the color get into the case?
Well, while the process itself is easy (you mix some powder together with the plastic pellets), this also needs quite a bit of preparing.
Depending on the plastic you use, you also need to use different color types.
Different types of plastic have different melting temperatures, so the powder you use has to be the correct one as well.
Otherwise, the color wouldn't melt or would burn. Both would lead to horrible results.
Also, you need to find the perfect mixture to make the color look good. This also depends on the wall thickness of the plastic part itself...
And as there are so many different types of colors available, the initial selection is very limited.
Usually, you get the typical industrial colors (bright red, yellow, green, etc.). For anything decent looking (a nice dark blue or red), you often need to get a customized color, made especially for you.
Additional stuff like a metallic look or the scratch resistant coating will also be included within that custom color.
Of course, custom colors need to be bought in higher quantities as well, and they take a while (3 - 7 weeks) before you get them from the manufacturer.
We will make samples in 5 different colors. To save costs and speed things up, we've decided to use 3 readily existing ones that look good and make 2 custom made ones. None of them will have any special coating or anything added, as that adds more costs and will take longer.
The mass produced case will have a nice, decent color with matte scratch resistant coating and maybe a tiny little bit of metallic (just to make the color look good, I'm not aiming for a metallic look!)
It could very well be we'll produce more than one color for mass production, but they will all have the matte scratch resistant coating.
As the plastic itself is colored, it can never rub off (though I doubt it would even rub off with that coating
)
Okay, so here is how we proceed from now on:
The mold for the lower part of the basement (with the battery compartment) is already finished.
The battery lid, LCD frame and keyboard main part mold will be finished end of next week.
They will then produce transparent physical testing versions of those parts and send them to me so I can test that everything fits and make sure the shoulder buttons, etc. are working fine.
This will only be a physical sample, it will use a cheap plastic and fast production run, it will not look pretty (so do not be scared when you see the pictures in 2 weeks
)
Once I confirm the samples to be working, these parts will immediately be produced with the chosen colors. These will look better than the physical sample, but not as good as the mass produced one as the scratch-resistant coating is still missing.
Of course, while I'm testing this part, the last two molds, the logo and the LCD backside will be finished (approx. 1 week as well), there won't be a break in the mass production.
They will also be produced in the chosen sample colors and then it's time to assemble the units for the prototype customers (who have given me their three favorite colors).
As soon as I make the decision about the final color (maybe you can help here at the boards
) or final colors, the custom color mix will be ordered, including the scratch-resistant coating any maybe some slight metallic look.
Once the colors have arrived, mass production can take place in any quantity.
2000 case sets would take approximately 1 week.
While all this is happening, Nikolaus and I will continue to work on the PCB testing and assembling as well as setting up the mass production with GC and ordering the parts once the hardware is confirmed to be working.
Okay, before we start, one more video of the current CNC Milling:
First you can see the final step of the tooling for the keyboard part. The copper slowly cuts into the metal using electricity.
That takes quite a while.
The second thing you can see is basically the LCD frame being "stamped" into the metal... you can imagine how long that takes.
It's a slow process, but the only way to do it accurately without any issues.
The last thing you can see is a typical CNC drill that mills into the metal block. That ALSO takes a while, as you can it is moving slowly.
Yes, creating molds suitable for plastic injection is a quite a lengthy job, if done right.
Altogether, the Pyra will have 7 molds.
Here are some more pictures of the same process. Sorry for the quality, I only had my mobile phone with me today
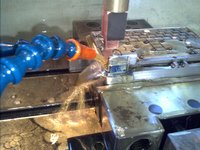

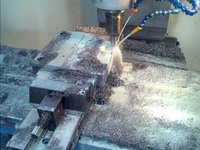
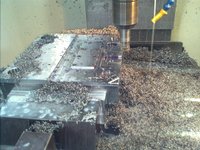
Okay, let's talk about the colors now!
So, the material we're using for the Pyra is the transparent one you've seen in the video yesterday... nearly unbreakable Polycarbonate.
How does the color get into the case?
Well, while the process itself is easy (you mix some powder together with the plastic pellets), this also needs quite a bit of preparing.
Depending on the plastic you use, you also need to use different color types.
Different types of plastic have different melting temperatures, so the powder you use has to be the correct one as well.
Otherwise, the color wouldn't melt or would burn. Both would lead to horrible results.
Also, you need to find the perfect mixture to make the color look good. This also depends on the wall thickness of the plastic part itself...
And as there are so many different types of colors available, the initial selection is very limited.
Usually, you get the typical industrial colors (bright red, yellow, green, etc.). For anything decent looking (a nice dark blue or red), you often need to get a customized color, made especially for you.
Additional stuff like a metallic look or the scratch resistant coating will also be included within that custom color.
Of course, custom colors need to be bought in higher quantities as well, and they take a while (3 - 7 weeks) before you get them from the manufacturer.
We will make samples in 5 different colors. To save costs and speed things up, we've decided to use 3 readily existing ones that look good and make 2 custom made ones. None of them will have any special coating or anything added, as that adds more costs and will take longer.
The mass produced case will have a nice, decent color with matte scratch resistant coating and maybe a tiny little bit of metallic (just to make the color look good, I'm not aiming for a metallic look!)
It could very well be we'll produce more than one color for mass production, but they will all have the matte scratch resistant coating.
As the plastic itself is colored, it can never rub off (though I doubt it would even rub off with that coating
Okay, so here is how we proceed from now on:
The mold for the lower part of the basement (with the battery compartment) is already finished.
The battery lid, LCD frame and keyboard main part mold will be finished end of next week.
They will then produce transparent physical testing versions of those parts and send them to me so I can test that everything fits and make sure the shoulder buttons, etc. are working fine.
This will only be a physical sample, it will use a cheap plastic and fast production run, it will not look pretty (so do not be scared when you see the pictures in 2 weeks
Once I confirm the samples to be working, these parts will immediately be produced with the chosen colors. These will look better than the physical sample, but not as good as the mass produced one as the scratch-resistant coating is still missing.
Of course, while I'm testing this part, the last two molds, the logo and the LCD backside will be finished (approx. 1 week as well), there won't be a break in the mass production.
They will also be produced in the chosen sample colors and then it's time to assemble the units for the prototype customers (who have given me their three favorite colors).
As soon as I make the decision about the final color (maybe you can help here at the boards
Once the colors have arrived, mass production can take place in any quantity.
2000 case sets would take approximately 1 week.
While all this is happening, Nikolaus and I will continue to work on the PCB testing and assembling as well as setting up the mass production with GC and ordering the parts once the hardware is confirmed to be working.