One week has passed since I returned from Greece, so it's time to let you know about the status of the cases!
As you might've read already (if you followed my updated on the last news thread), the movement was a success!
The moulds are already being worked on at the new company and the produced plastic shells are also in my hands.
Here are some pictures of the produced shells:
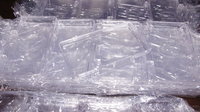
Theae are the main parts of the case. Yeah, the packaging (wrappigg up) is a bit weird, the new company will do that differently.
Here are the small plastic parts (in bags):
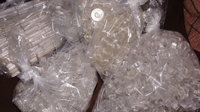
And finally, the rubber parts to keep the speakers in place:
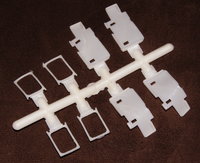
These are about 100 sets - that's all they did produced until now.
These will be used by me to assemble the prototypes (hopefully this week, when I find the time) and I'll put these sets on sale as well.
So, what's wrong with them?
They're mostly fine but have the following two main issues:
1. The lower part (with the battery compartment) is a tiny bit warped and not 100% flat
2. The keyboard part is missing some pegs which make sure the PCB stays in the proper position and can't wiggle around.
The first one isn't that bad and doesn't affect the usabilty at all (you won't even notice it unless you take a closer look) and the second one is actually the reason the shoulder buttons don't work properly on all units:
These missing pegs make sure that the PCB sits perfectly inside the case. Even without a keymat, it stays fixed and can't move around. The Pandora case has these as well.
As these are MISSING, the PCB isn't fixed. It's squeezed in between the keymat and the battery compartment - and the position changed depending on how much you tighten the screws.
The effect is clear: Depending on the position, the shoulder buttons hit the buttons on the PCB - or miss them.
That's the reason the shoulder buttons worked fine with some units but not with others.
This CAN be manually fixed on the existing cases - but that's not suitable for mass production (of course!).
So yes, these can be used for prototypes (and if you want to play around with them a bit).
What about the moulds themselves? Are they fine? What needs to be fixed?
Well, I already took the time to take a look at the moulds together with the new company:
Luckily, it's nothing too serious and they're already working on applying fixes.
Some information about colors:
In theory, the cases can be produced in ANY color we can think of.
However, any custom color needs to be mixed, which means that it can take a few weeks AND we'd have to buy at least a ton of the plastic material.
So while that's a possibility, it does make more sense getting a color that's currently on stock, as this one doesn't need to be produced and is available with any quantity right away.
The good thing is: The company where they buy their color materials is pretty big - and has a LOT of customers. So they have quite a lot of different colors readily available!
They will send me a list of those (RAL colors) and then we can produce samples.
So the steps for the cases:
Once that's done, it's a lot easier to make assumptions.
But they want to work as fast as possible on that, so it should be a LOT faster than what we've seen the last 2 years...
Now, I also took some pictures of the moulds, in case you're interested. Sorry for some being blurry - I only had a smartphone available and it didn't want to focus properly.
One mould always consists of two parts: An upper and a lower one. So I'll show you both.
The keyboard part:
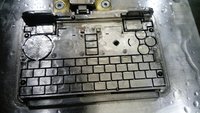
The discs for the nubs:
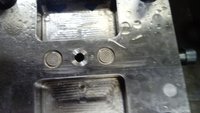
Logo, Stylus holder, stylus and an unused DPad (as the DPad is coming from the keymat company):
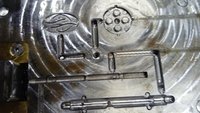
This is - of course - the lid with the hole for the logo plate:
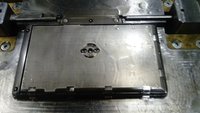
The bottom part with the battery compartment:
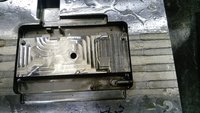
The shoulder buttons:
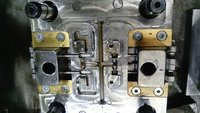
The rubbers for the speakers:
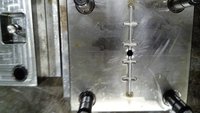
The battery cover as well as the frame for the LCD:
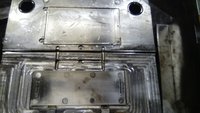
Quite a few moulds
That's it for today. I'll try to find some time to post another thread to let you know the status of EVERTHING regarding the Pyra (not only the cases) soon, but it's 5am here and I'm tired, so it won't be now
As you might've read already (if you followed my updated on the last news thread), the movement was a success!
The moulds are already being worked on at the new company and the produced plastic shells are also in my hands.
Here are some pictures of the produced shells:
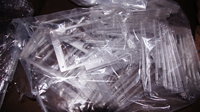
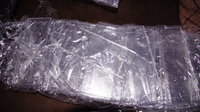
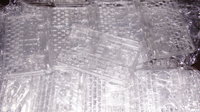
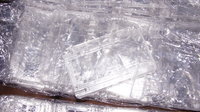
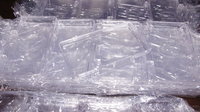
Theae are the main parts of the case. Yeah, the packaging (wrappigg up) is a bit weird, the new company will do that differently.
Here are the small plastic parts (in bags):
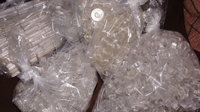
And finally, the rubber parts to keep the speakers in place:
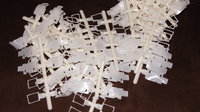
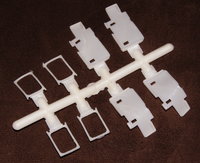
These are about 100 sets - that's all they did produced until now.
These will be used by me to assemble the prototypes (hopefully this week, when I find the time) and I'll put these sets on sale as well.
So, what's wrong with them?
They're mostly fine but have the following two main issues:
1. The lower part (with the battery compartment) is a tiny bit warped and not 100% flat
2. The keyboard part is missing some pegs which make sure the PCB stays in the proper position and can't wiggle around.
The first one isn't that bad and doesn't affect the usabilty at all (you won't even notice it unless you take a closer look) and the second one is actually the reason the shoulder buttons don't work properly on all units:
These missing pegs make sure that the PCB sits perfectly inside the case. Even without a keymat, it stays fixed and can't move around. The Pandora case has these as well.
As these are MISSING, the PCB isn't fixed. It's squeezed in between the keymat and the battery compartment - and the position changed depending on how much you tighten the screws.
The effect is clear: Depending on the position, the shoulder buttons hit the buttons on the PCB - or miss them.
That's the reason the shoulder buttons worked fine with some units but not with others.
This CAN be manually fixed on the existing cases - but that's not suitable for mass production (of course!).
So yes, these can be used for prototypes (and if you want to play around with them a bit).
What about the moulds themselves? Are they fine? What needs to be fixed?
Well, I already took the time to take a look at the moulds together with the new company:
- The quality itself is fine. FormAction did a good job here, so nothing to worry about here.
- The missing plastic pegs mentioned above need to bee added in order to keep the PCB in the proper position. The interesting thing is that these pegs are actually existing in the 3D data - so my 3D printed cases didn't have these issues! They are simply missing in the mould!
A mould is negative (as plastic is injected in there), therefore, adding pegs means removing metal inside the mould. This is way easier than removing something, so not a big challenge. - The shoulder buttons will be checked and improved once the PCB is sitting in proper position. They might already be perfectly fine, we'll see once that first fix has been applied.
- The injection points of some of the moulds will be adjusted and improved. What does that mean? Well, during production, hot liquid plastic is being injected with some pressure into the mould, completely filling it out. Once it cools down, the plastic part is done. However, if there's an area where the plastic flow is a bit slower or faster than in other areas or it cools off too fast, you will have some effects like discolorization, brittle plastic or shrinking marks or (in worst case), some parts aren't even filled with plastic so you will have an incomplete part.
This is the reason we painted the Pandora cases (discolorizations) and it's tricky to get this right.
The expert from the new company looked at the moulds and already described exactly what problems our colored cases most likely had (without having even seen them!) and that this can be fixed with a proper fix to the injection points. He also pointed out that one or two moulds probably won't even work properly with the currently set injection points and that most of the cases produced with these would would not be usable... that would totally explain why FA only produced 100 set so far and why they wanted to increase the price per set A LOT for the actual mass production run.
Luckily, it's nothing too serious and they're already working on applying fixes.
Some information about colors:
In theory, the cases can be produced in ANY color we can think of.
However, any custom color needs to be mixed, which means that it can take a few weeks AND we'd have to buy at least a ton of the plastic material.
So while that's a possibility, it does make more sense getting a color that's currently on stock, as this one doesn't need to be produced and is available with any quantity right away.
The good thing is: The company where they buy their color materials is pretty big - and has a LOT of customers. So they have quite a lot of different colors readily available!
They will send me a list of those (RAL colors) and then we can produce samples.
So the steps for the cases:
- The plastic pegs will be added, some mould injection points which will certainly lead to issues will be fixed (this is already being worked on)
- Each plastic part will be produced with some cheap material. The reason for that? Well, if the CHEAP material works fine already, then a good one won't have any issues. And if the cheap one shows some problems, you know exactly where and what to fix. So basically, this is being done to make the optimize the injection points as good as possible.
- The shoulder buttons will be checked with the fixed cases and be tweaked if need be (it could be they work out of the box).
- Samples will be produced in the colors I choose.
- That's it - time for mass production!
Once that's done, it's a lot easier to make assumptions.
But they want to work as fast as possible on that, so it should be a LOT faster than what we've seen the last 2 years...
Now, I also took some pictures of the moulds, in case you're interested. Sorry for some being blurry - I only had a smartphone available and it didn't want to focus properly.
One mould always consists of two parts: An upper and a lower one. So I'll show you both.
The keyboard part:
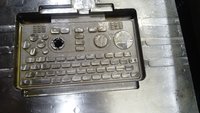
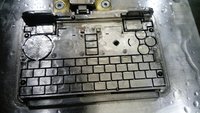
The discs for the nubs:
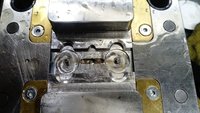
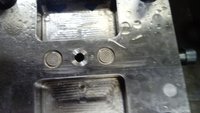
Logo, Stylus holder, stylus and an unused DPad (as the DPad is coming from the keymat company):

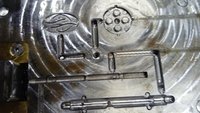
This is - of course - the lid with the hole for the logo plate:
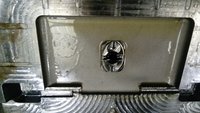
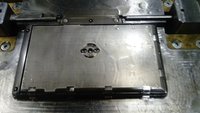
The bottom part with the battery compartment:
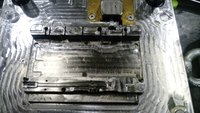
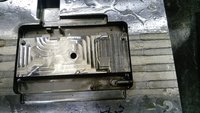
The shoulder buttons:
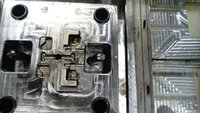
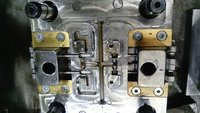
The rubbers for the speakers:
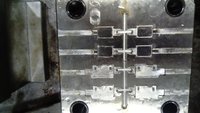
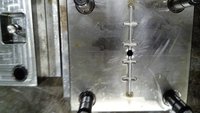
The battery cover as well as the frame for the LCD:
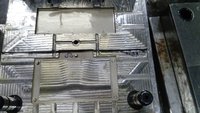
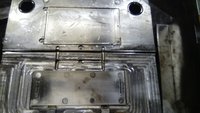
Quite a few moulds
That's it for today. I'll try to find some time to post another thread to let you know the status of EVERTHING regarding the Pyra (not only the cases) soon, but it's 5am here and I'm tired, so it won't be now
Last edited: