Some quick update from me, this time with a new thread (as I don't want to hide that in the prototype assembly thread).
1. Prototype Assembly
I have ordered more material for cutting the heatpipes as well as more heatsinks but am still waiting for them.
They should hopefully arrive next week and then the assembly should be finished pretty quickly.
2. Other stuff I'm working on
In the meantime, I have started to look for companies that can produce custom heatsinks. While the standard one we used so far fits well, we still have 1.5mm more space for the width, so a custom made could improve things a bit.
If the price for doing a custom one is reasonable, then I'll do that. If not, I can always buy the standard ones
If you know of a company who does stuff like that (would be best here in Europe) and you know they are doing a good job and have reasonable prices, let me know
We're also looking inf different ways to properly apply the logo and metal plate. Glueing them manually is tedious. It would be best if the logos had some self-adhesive 3M glue on them, as it holds pretty well and it would only take seconds to apply them. The problem is: Right now they're laser-cut - but that would melt the glue
So we might need to punch them out, this would probably be the best way
3. Status of the case improvements
I am happy to report that the main fixes on the cases have been done!
Mostly production related fixes, except for adding springs to the shoulder buttons, which has already been done in the mould:
A set of cases will be produced today and shipped to me.
There are still some smaller things I've noted down during assembly:
Even if the case itself work fine, there are some things you notice when you're assembling multiple units at once. Small stuff that slows you down (for example, putting ont he speaker sealing correctly, sliding the LCD cable through the hinge, etc.) and would cost more in production.
I've checked these and tried to find better solutions, and often it's just a tiny little thing that needs to be changed to fix that. I'm recording all this properly on video, so the guys working on the case can see what the issue is. I also present my idea how to fix it, but they also think about it and might find some better ideas (they have experience with stuff like that).
Recording that properly and showing exactly what the problem is takes a bit of time, so it's a slow process.
But it will REALLY speed up things when it comes to mass assembly!
Once I receive the case and the team sees my videos, I'll do a video conference with them to discuss any final tweaks that still remains. If all major issues have been fixed, the case is basically a finished Rev 1.0 which is fully usable
It's really refreshing to see how things are now moving again, after the case hasn't really been worked on for the last 1.5 years...
4. The keymat
As previously mentioned, glueing the keys didnt't work without bubbles.
I'm happy to report that the new keycaps which don't need to be glued have been finished
They look like this:
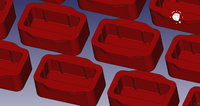
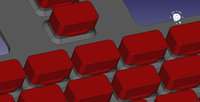
As you can see, they now have small pegs inside so they will tightly sit on the rubber mat.
Additionally, they have some frame around them, so they will sit properly inside the case. They can't come loose and won't fall out, but in theory, it's possible for you to remove the caps and paint onto your keys to change the layout (though that changed key won't be backlit of course).
So, done and fixed.
The main slowness right now is probably still myself, for various reasons.
I am still doing things at a bit slower pace, as I really overdid it in December / January, which lead to a lack of motivation - and that's the least thing we need right now.
Secondly, the Pyra cost A LOT MORE MONEY than planned, so money is tight and I need to make sure the shop pulls in enough money to keep the company going. So I cannot simply abandon the shop for a week to fulltime work on the Pyra. Would be great, but it wouldn't work out.
And thirdly, my main profession is not designing and developing such products. When I need something like a custom heatsink, I first need to go and search for a proper companies. WIth some stuff, I don't even know the correct search term to find a company for that (example: I am thinking of maybe use some pre-cut self-adhesive tape for sealing the speakers, you know, the 0.2 - 0.3mm thin one that you simply put on and that's it. Probably the fastest and most secure way when mass assembling the units. A thin self-adhesive sticker, punched based on our own design. Something that can be seen in tons of devices, so pretty easy and common to get, right? Well... try to find a company for that. I still don't know what's the best search term to use to find one...).
It's tiny stuff like that - things you never imagined would steal your time - that slows you down.
But yeah, if you know of such a company... let me know
I found one in Germany so far, but I'm happy for more options 
Well, and hockey season is over for our team, so I have a bit more time available from now on.
But yeah, blame it on me now
5. Current Roadmap
As a summary (or if you didn't want to read through the whole text), here's my current roadmap (with no time given, as usual).
As usual, any questions, remarks, blaming, shouting and screaming, insulting, etc.: Post here at the thread
1. Prototype Assembly
I have ordered more material for cutting the heatpipes as well as more heatsinks but am still waiting for them.
They should hopefully arrive next week and then the assembly should be finished pretty quickly.
2. Other stuff I'm working on
In the meantime, I have started to look for companies that can produce custom heatsinks. While the standard one we used so far fits well, we still have 1.5mm more space for the width, so a custom made could improve things a bit.
If the price for doing a custom one is reasonable, then I'll do that. If not, I can always buy the standard ones
If you know of a company who does stuff like that (would be best here in Europe) and you know they are doing a good job and have reasonable prices, let me know
We're also looking inf different ways to properly apply the logo and metal plate. Glueing them manually is tedious. It would be best if the logos had some self-adhesive 3M glue on them, as it holds pretty well and it would only take seconds to apply them. The problem is: Right now they're laser-cut - but that would melt the glue
So we might need to punch them out, this would probably be the best way
3. Status of the case improvements
I am happy to report that the main fixes on the cases have been done!
Mostly production related fixes, except for adding springs to the shoulder buttons, which has already been done in the mould:
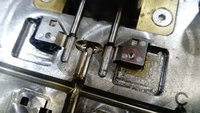
A set of cases will be produced today and shipped to me.
There are still some smaller things I've noted down during assembly:
Even if the case itself work fine, there are some things you notice when you're assembling multiple units at once. Small stuff that slows you down (for example, putting ont he speaker sealing correctly, sliding the LCD cable through the hinge, etc.) and would cost more in production.
I've checked these and tried to find better solutions, and often it's just a tiny little thing that needs to be changed to fix that. I'm recording all this properly on video, so the guys working on the case can see what the issue is. I also present my idea how to fix it, but they also think about it and might find some better ideas (they have experience with stuff like that).
Recording that properly and showing exactly what the problem is takes a bit of time, so it's a slow process.
But it will REALLY speed up things when it comes to mass assembly!
Once I receive the case and the team sees my videos, I'll do a video conference with them to discuss any final tweaks that still remains. If all major issues have been fixed, the case is basically a finished Rev 1.0 which is fully usable
It's really refreshing to see how things are now moving again, after the case hasn't really been worked on for the last 1.5 years...
4. The keymat
As previously mentioned, glueing the keys didnt't work without bubbles.
I'm happy to report that the new keycaps which don't need to be glued have been finished
They look like this:
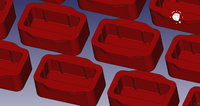
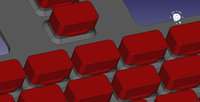
As you can see, they now have small pegs inside so they will tightly sit on the rubber mat.
Additionally, they have some frame around them, so they will sit properly inside the case. They can't come loose and won't fall out, but in theory, it's possible for you to remove the caps and paint onto your keys to change the layout (though that changed key won't be backlit of course).
So, done and fixed.
The main slowness right now is probably still myself, for various reasons.
I am still doing things at a bit slower pace, as I really overdid it in December / January, which lead to a lack of motivation - and that's the least thing we need right now.
Secondly, the Pyra cost A LOT MORE MONEY than planned, so money is tight and I need to make sure the shop pulls in enough money to keep the company going. So I cannot simply abandon the shop for a week to fulltime work on the Pyra. Would be great, but it wouldn't work out.
And thirdly, my main profession is not designing and developing such products. When I need something like a custom heatsink, I first need to go and search for a proper companies. WIth some stuff, I don't even know the correct search term to find a company for that (example: I am thinking of maybe use some pre-cut self-adhesive tape for sealing the speakers, you know, the 0.2 - 0.3mm thin one that you simply put on and that's it. Probably the fastest and most secure way when mass assembling the units. A thin self-adhesive sticker, punched based on our own design. Something that can be seen in tons of devices, so pretty easy and common to get, right? Well... try to find a company for that. I still don't know what's the best search term to use to find one...).
It's tiny stuff like that - things you never imagined would steal your time - that slows you down.
But yeah, if you know of such a company... let me know
Well, and hockey season is over for our team, so I have a bit more time available from now on.
But yeah, blame it on me now
5. Current Roadmap
As a summary (or if you didn't want to read through the whole text), here's my current roadmap (with no time given, as usual).
- I'll cut the heatsink material as soon as it arrives and finish assembling the prototypes.
- I'll test the prototypes and finally ship them out
- Case Company finishes the first set of cases today and will send it to me (with all major fixes done and an improved shoulder button which uses a spring)
- I'll discuss final possible non-mandatory tweaks with the case company.
- If functionality of the prototypes is confirmed, mass production of PCBs is beind ordered (this will take around 6 - 8 weeks)
- Heatsink material and maybe proper heatsinks are being produced
- Cases are being produced
- Keymats arrive
- Mass production happens
As usual, any questions, remarks, blaming, shouting and screaming, insulting, etc.: Post here at the thread