Assembled 7 Prototype Pyras tonight.
Works pretty well.
After I assembled 2 or 3 I found the best and fastest way to assemble them, and it's less than 10 minutes you need for a full assembly
For those who are interested in the optimized steps:

Pretty weird putting the LCD in last (if you assembled hundreds of Pandoras before), but it works best
Some more information about the case (shrinking marks, etc.):
The current material that has been used is some black material they had available from some other mass production.
That's the reason we have some discolorization and shrinking marks there.
There are materials which are optimized for various mold flows. Depending on the material, it's thicker or more liquid, it needs more or less heat.
For small details, you need a material that is very liquid and cools off evenly - there is special material for that, that is mostly suited and being used for mobile devices.
The manufacturer of that material already has the 3D data to analyze the mold flow and mix a perfect material for that.
This takes a few weeks though, so the current cases have been made with an unoptimized material that's too thick.
This leads to the shrinking marks. Those will be gone once the final material arrives
So, what important stuff did I find out while assembling the Pyras?
Overall, the case is now physically perfect.
The only small thing are still the shoulder buttons - but that shouldn't be a big deal:
With 3 out of the 7 Pyras, all shoulder buttons work perfectly. The other 4 work, but don't feel as good as they should.
The reason for that is simple: We need a bit more tolerance (which means: We need to remove a tiny bit of plastic).
While the buttons are very accurate on the PCB, they still have a tolerance of about 0,2mm. The case currently doesn't take that into account and stops the button too early sometimes.
Just removing a bit of plastic there fixes that.
Everything else is fine though, which is awesome
The LCD Cable also has the perfect length, another step done.
These can now go into mass production as well.
Speaker sealing: While the silicon idea is basically a good idea, I'm not sure it closes everything perfectly...
This needs to be tested. It might be better using the same shape and plot that out of thin self-adhesive tape.
This would make sure the sealing is perfect.
I have to do some more testing soon!
Sooooo we're getting there.
Quick summary:
Don't expect your final units within the next few weeks, but we're continuously moving forward
Works pretty well.
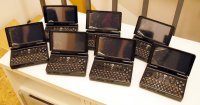
After I assembled 2 or 3 I found the best and fastest way to assemble them, and it's less than 10 minutes you need for a full assembly
For those who are interested in the optimized steps:
- Roll the LCD Cable and put it through the lower lid part.
- Put the hinge part into the keyboard part.
- Slide the LCD Cable through the keyboard lid and put the lid part into the keyboard part.
- Lock the hinge. Then you have the keyboard part and the lid part fully assembled including the rolled LCD cable.
- Put in the speakers, sealing, nub discs and keymat.
- Put in the PCB, connect the LCD Cable.
- Put the stylus holder and the shoulder buttons into the bottom part.
- Put the aluminium plate (for cooling) onto the PCB.
- Assemble the bottom part with the keyboard part, screw it together, insert stylus.
- Assemble the LCD with the Display board (two plugs, one for the LCD, one the the touchscreen)
- Connect the display board to the LCD Cable.
- Put the LCD + Displayboard into the lid, put the frame on top. Screw it on.
Pretty weird putting the LCD in last (if you assembled hundreds of Pandoras before), but it works best
Some more information about the case (shrinking marks, etc.):
The current material that has been used is some black material they had available from some other mass production.
That's the reason we have some discolorization and shrinking marks there.
There are materials which are optimized for various mold flows. Depending on the material, it's thicker or more liquid, it needs more or less heat.
For small details, you need a material that is very liquid and cools off evenly - there is special material for that, that is mostly suited and being used for mobile devices.
The manufacturer of that material already has the 3D data to analyze the mold flow and mix a perfect material for that.
This takes a few weeks though, so the current cases have been made with an unoptimized material that's too thick.
This leads to the shrinking marks. Those will be gone once the final material arrives
So, what important stuff did I find out while assembling the Pyras?
Overall, the case is now physically perfect.
The only small thing are still the shoulder buttons - but that shouldn't be a big deal:
With 3 out of the 7 Pyras, all shoulder buttons work perfectly. The other 4 work, but don't feel as good as they should.
The reason for that is simple: We need a bit more tolerance (which means: We need to remove a tiny bit of plastic).
While the buttons are very accurate on the PCB, they still have a tolerance of about 0,2mm. The case currently doesn't take that into account and stops the button too early sometimes.
Just removing a bit of plastic there fixes that.
Everything else is fine though, which is awesome
The LCD Cable also has the perfect length, another step done.
These can now go into mass production as well.
Speaker sealing: While the silicon idea is basically a good idea, I'm not sure it closes everything perfectly...
This needs to be tested. It might be better using the same shape and plot that out of thin self-adhesive tape.
This would make sure the sealing is perfect.
I have to do some more testing soon!
Sooooo we're getting there.
Quick summary:
- LCD Cable: Done now as well, ready for mass production.
- Case: Done, except for minor tweaks in the shoulder buttons. Otherwise ready for mass production.
- LCDs: Already mass produced, including touchscreen.
- Batteries: Already mass produced
- Keymat: Samples of the (most probably) final revision are currently being produced.
- Aluminium Plate (for cooling): Will work on that this week.
- PCBs: Except for testing the fixes and work on the 4GB ones, they're ready for mass production as well. Nikolaus is working on that, now that he has cases
- Boxes: Basically finished, needs box design
. Production time is two weeks.
- Manual: Needs to be written, but I'll base it on Pandoras manual. Production time is one week.
- OS: Basic Debian is working, but a lot of low-level stuff needs to be done... remember the first OS for the Pandora? Yep, something like that
Don't expect your final units within the next few weeks, but we're continuously moving forward