First day here in Greece is over. Quite a shocking start, but a lot more confidence in the afternoon.
What happened?
Read on
With spicy pictures and news 
Let's first start with the shock. You'll hate this. I hated this:
I can't show you a finished case set. I didn't get one. All I got was one ugly looking basement part.
Looks similar to the first Pandora case without paint we got... what a start of the day.
You can take a look here:
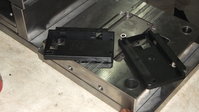
Ugly, isn't it? Well, yes, it is. And it was the start of me learning how plastic mould injection is working in detail.
It's quite complex. But I've learnt so much new things today! And I'll try to tell it to you as good as I can
So, why did they tell me they've got a full set for me?
Because they have. Not a full set of finished cases - but a full set of the molds. I simply understood that wrong. Probably combined with the anticipation of getting a final case
What they have is the first step of the molds, to be exact: They're done, you could produce cases with them them, but they have no tweaks applied yet and no surface modification.
This probably is comparable to the final molds we got for the Pandora: Physically, they were correct, but they had shrinking marks (as they weren't tweaked yet) and they didn't have a surface modification, so they looked ugly (and we decided to paint them...)
So our step 1 here was basically the final step of the Pandora molds.
Here is a basic overview how plastic mold injection works (use the spoiler to reveal it):
Okay, so as mentioned, the basic molds are finished, currently they are tweaking them to make sure they don't have any issues as well as applying smooth surfaces on top.
One mold (the lower part of the basement, with the battery compartment) will be completely finished tomorrow (though I don't know if it's still in time so I can at least take one sample with me).
The mold for the top side (the keyboard area) will be finished until end of next week.
Then we'll have a complete base to test.
Next will be the shoulder buttons (so we can test those, as these are the parts with the lowest tolerances), and after that, the lid will be finished.
Then we got a full set!
They will produce samples shortly after each mold is finished, so I will get regular shipments of new sample parts regularly until the set it complete.
The samples I get will be dark transparent which helps finding out any issues, as you can see if some parts don't fit properly.
When I've tested and approved everything, the cases will be produced in various colors.
We've chosen about 10 colors to try out (so the prototype buyers will get one of their favorite case colors as well!) and then it's time to choose the mass production colors... then we're done here.
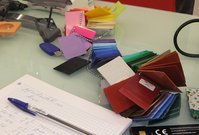
We've also decided on the plastic we'll use.
The base plastic is transparent, but by adding pulverized color, it will be completely opaque in that color.
The material is very flexible and durable. If you bend it, it doesn't break but immediately move back into it's original position.
According to the manufacturer, it is bulletproof (though I will NOT suggest you test that...)
I've captured a bit of the durability test using my camera... though I missed the best part: someone jumping on that plastic part, and the small hook you can see on the case didn't break.
Should be good enough for the battery lid, eh?
BTW: A quick physical test of the ugly-produced base part was successful.
I could put in the mainboard, insert a battery (and got some LEDs light up, so it works) and opening / closing the simcard as well as the MicroSD-card slot worked as well.
Here is the small video, first showing a bit of the production of the keyboard mold as well as the durability test of the plastic we've chosen.
Phewww, what a day.
I am sure you can imagine how shocked I was at the beginning, learning that I won't have a full set to assemble here, and the one part I've seen was ugly... but learning about all that above was interesting.
And it was really a good thing I came here, to decide about the material surface, the plastic and the color!
I hope you enjoyed the newspost, even though it was looooong and too much to read, probably
Well, here are some more pictures showing molds and tools.
You can also download them as 3D MPO files, if you got something to look at them in real 3D
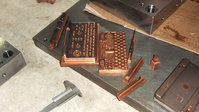
What happened?
Read on
Let's first start with the shock. You'll hate this. I hated this:
I can't show you a finished case set. I didn't get one. All I got was one ugly looking basement part.
Looks similar to the first Pandora case without paint we got... what a start of the day.
You can take a look here:
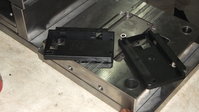
Ugly, isn't it? Well, yes, it is. And it was the start of me learning how plastic mould injection is working in detail.
It's quite complex. But I've learnt so much new things today! And I'll try to tell it to you as good as I can
So, why did they tell me they've got a full set for me?
Because they have. Not a full set of finished cases - but a full set of the molds. I simply understood that wrong. Probably combined with the anticipation of getting a final case
What they have is the first step of the molds, to be exact: They're done, you could produce cases with them them, but they have no tweaks applied yet and no surface modification.
This probably is comparable to the final molds we got for the Pandora: Physically, they were correct, but they had shrinking marks (as they weren't tweaked yet) and they didn't have a surface modification, so they looked ugly (and we decided to paint them...)
So our step 1 here was basically the final step of the Pandora molds.
Here is a basic overview how plastic mold injection works (use the spoiler to reveal it):
1. 3D Design
The first thing is the 3D design. CAD. That's the 3D model where we got the renderings from.
2. Creating the molds
Then you need to turn these models into molds. And THAT'S a very tricky part.
If you think it's comparable to 3D printing: Nope, it isn't. Totally different.
A mold is basically like a box:
You close it and pump hot plastic into it. It then cools off and gets hard. Then your plastic part is done.
So the mold needs to be a negative (inverted version) of the plastic part, enclosed in two metal parts.
No problem for simple parts (like the LCD frame of the lid). It gets trickier with more complex parts though, like the keyboard part of the case: There are holes in the area where the hinge is. Holes inverted mean: The Metal needs to float in the air! You cannot create such a complex part with fine details (metal still needs to be CNC-milled, after all), so you need to create another part for the mold that you can put inside when you assemble the mold.
With complex parts, the mold is a bit like a puzzle, with various inlays to create the inside-holes and special shapes.
That's also needed for the clips of the battery lid, for example.
You can see the cut metal where the additional tools for creating the clips will be put in on this photo:
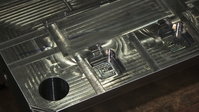
When 3D printing, you have your 3D data in the computer and tell it to print it out.
With mold creation, you need to first think how to achieve what you need and then create the molds including various additional tools with a CNC mill.
However, that's not the only complex thing.
CNC milling the steel molds is not accurate enough for fine details like the grid for the keyboard part.
You need to create ANOTHER tool to do slow, and slowly cut them directly into the hot steel (with permanent oil cooling).
You can see that in the picture here (and also in the video below):
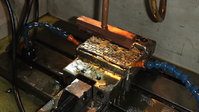
Creating ONE row of these key rows takes approximately five hours.
In the end, however, you will have nice, clean and perfect steel mold that can be used for about 1 Million cases...
Now I can totally understand why mold production is very cheap in China, but very expensive in most parts of Europe: It's a LOT of labour work - and wages are usually very high in Europe.
A full case set like the one from the Pyra takes a couple of months until it's finished.
3. Testing and tweaking the molds
Creating the molds is already a complex thing, but it doesn't automatically mean they will be perfect right away.
Similar to tweaking the machine file and PCB layout for pick & place mass production (which is what we did the pre-production run at Global Components for), you also need to test and tweak the molds.
Producing plastic works like this:
Melted plastic is pumped into the mold and there it cools off. The important thing is that it EVENLY cools.
Otherwise, various problems can occur: Color differences, areas where it automatically can develop cracks after a while (remember the Pandora?) shrinking marks or slightly bent parts.
Imagine, for example, that you have a huge peg in the case. If that one cools off faster than the ground plane, then the weight pushes it down and affects the still melted plastic - that's something that can be seen on many cheap plastic parts.
Also, when cooling off, the plastic can also shrink a bit, so the size is a tiny bit different than in your model.
This is also something you need to test and then fix in the mold.
I am almost sure that was the problem with the LCD frame of the Pandora, the reason why the lower side has such a gap: The outer link shrank a bit and hasn't been tweaked, therefore the frame is being pushed together from both sides resulting in the gap.
While the mold flow can be simulated to some extents, it's nigh impossible to accurately simulate it.
So you need experience (to choose the correct places to inject the plastic before creating the mold) and need to analyse the produced parts, doing small tweaks to the molds or the machine program (you can change the pressure and heat for the plastic injection, which also improves things).
4. Creating the material surface
After everything has been tweaked so that the molds are basically ready to produce the plastic parts, you should improve the look of the plastic by applying some material surface to the mold.
Otherwise, the plastic will simply look plain and glossy (and totally ugly), and it easily receives scratches.
By applying material surface, you can create a smooth surface on the plastic that makes it look matte and it even covers smaller issues (small shrinking marks you can't prevent).
We will use a very smooth surface for the Pyra, which gives it a nice, matte look.
Here is a mold which already has the material surface applied:
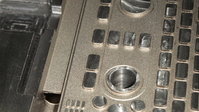
You get this effect by eroding the mold. The finer you want it, the longer it takes. That part needed about 30 hours, just for the material surface!
5. Plastic injection!
Finally, once the molds are finished, the plastic injection can happen!
That's pretty straightforward (as it usually is when you do mass production, mass production has to be well prepared, simple and reliable to prevent huge failures).
The plastic we use is a fully transparent one (the same one you can see in the video below) and by adding some pulverized color, you create the color you want.
Once the molds are finished, thousands of case sets can easily be produced within a few days.
Except you want...
6. Special treatment afterwards
Some things like a scratch-resistant coating can directly be applied at FormAction (so that won't need much more), but some effects are being done with a partner company, for example, textures on the case like these:
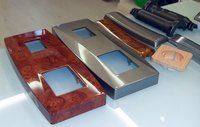
Yes, we will produce some units looking like these - but those will be special editions, as it add approximately 30 EUR to production costs on top!
It's cool seeing what's possible though!
So much for our small introduction to mold injection... let's continue with our plans.
The first thing is the 3D design. CAD. That's the 3D model where we got the renderings from.
2. Creating the molds
Then you need to turn these models into molds. And THAT'S a very tricky part.
If you think it's comparable to 3D printing: Nope, it isn't. Totally different.
A mold is basically like a box:
You close it and pump hot plastic into it. It then cools off and gets hard. Then your plastic part is done.
So the mold needs to be a negative (inverted version) of the plastic part, enclosed in two metal parts.
No problem for simple parts (like the LCD frame of the lid). It gets trickier with more complex parts though, like the keyboard part of the case: There are holes in the area where the hinge is. Holes inverted mean: The Metal needs to float in the air! You cannot create such a complex part with fine details (metal still needs to be CNC-milled, after all), so you need to create another part for the mold that you can put inside when you assemble the mold.
With complex parts, the mold is a bit like a puzzle, with various inlays to create the inside-holes and special shapes.
That's also needed for the clips of the battery lid, for example.
You can see the cut metal where the additional tools for creating the clips will be put in on this photo:
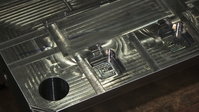
When 3D printing, you have your 3D data in the computer and tell it to print it out.
With mold creation, you need to first think how to achieve what you need and then create the molds including various additional tools with a CNC mill.
However, that's not the only complex thing.
CNC milling the steel molds is not accurate enough for fine details like the grid for the keyboard part.
You need to create ANOTHER tool to do slow, and slowly cut them directly into the hot steel (with permanent oil cooling).
You can see that in the picture here (and also in the video below):
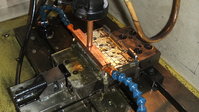
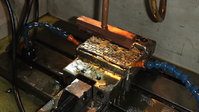
Creating ONE row of these key rows takes approximately five hours.
In the end, however, you will have nice, clean and perfect steel mold that can be used for about 1 Million cases...
Now I can totally understand why mold production is very cheap in China, but very expensive in most parts of Europe: It's a LOT of labour work - and wages are usually very high in Europe.
A full case set like the one from the Pyra takes a couple of months until it's finished.
3. Testing and tweaking the molds
Creating the molds is already a complex thing, but it doesn't automatically mean they will be perfect right away.
Similar to tweaking the machine file and PCB layout for pick & place mass production (which is what we did the pre-production run at Global Components for), you also need to test and tweak the molds.
Producing plastic works like this:
Melted plastic is pumped into the mold and there it cools off. The important thing is that it EVENLY cools.
Otherwise, various problems can occur: Color differences, areas where it automatically can develop cracks after a while (remember the Pandora?) shrinking marks or slightly bent parts.
Imagine, for example, that you have a huge peg in the case. If that one cools off faster than the ground plane, then the weight pushes it down and affects the still melted plastic - that's something that can be seen on many cheap plastic parts.
Also, when cooling off, the plastic can also shrink a bit, so the size is a tiny bit different than in your model.
This is also something you need to test and then fix in the mold.
I am almost sure that was the problem with the LCD frame of the Pandora, the reason why the lower side has such a gap: The outer link shrank a bit and hasn't been tweaked, therefore the frame is being pushed together from both sides resulting in the gap.
While the mold flow can be simulated to some extents, it's nigh impossible to accurately simulate it.
So you need experience (to choose the correct places to inject the plastic before creating the mold) and need to analyse the produced parts, doing small tweaks to the molds or the machine program (you can change the pressure and heat for the plastic injection, which also improves things).
4. Creating the material surface
After everything has been tweaked so that the molds are basically ready to produce the plastic parts, you should improve the look of the plastic by applying some material surface to the mold.
Otherwise, the plastic will simply look plain and glossy (and totally ugly), and it easily receives scratches.
By applying material surface, you can create a smooth surface on the plastic that makes it look matte and it even covers smaller issues (small shrinking marks you can't prevent).
We will use a very smooth surface for the Pyra, which gives it a nice, matte look.
Here is a mold which already has the material surface applied:
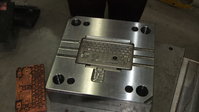
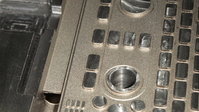
You get this effect by eroding the mold. The finer you want it, the longer it takes. That part needed about 30 hours, just for the material surface!
5. Plastic injection!
Finally, once the molds are finished, the plastic injection can happen!
That's pretty straightforward (as it usually is when you do mass production, mass production has to be well prepared, simple and reliable to prevent huge failures).
The plastic we use is a fully transparent one (the same one you can see in the video below) and by adding some pulverized color, you create the color you want.
Once the molds are finished, thousands of case sets can easily be produced within a few days.
Except you want...
6. Special treatment afterwards
Some things like a scratch-resistant coating can directly be applied at FormAction (so that won't need much more), but some effects are being done with a partner company, for example, textures on the case like these:
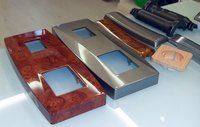
Yes, we will produce some units looking like these - but those will be special editions, as it add approximately 30 EUR to production costs on top!
It's cool seeing what's possible though!
So much for our small introduction to mold injection... let's continue with our plans.
Okay, so as mentioned, the basic molds are finished, currently they are tweaking them to make sure they don't have any issues as well as applying smooth surfaces on top.
One mold (the lower part of the basement, with the battery compartment) will be completely finished tomorrow (though I don't know if it's still in time so I can at least take one sample with me).
The mold for the top side (the keyboard area) will be finished until end of next week.
Then we'll have a complete base to test.
Next will be the shoulder buttons (so we can test those, as these are the parts with the lowest tolerances), and after that, the lid will be finished.
Then we got a full set!
They will produce samples shortly after each mold is finished, so I will get regular shipments of new sample parts regularly until the set it complete.
The samples I get will be dark transparent which helps finding out any issues, as you can see if some parts don't fit properly.
When I've tested and approved everything, the cases will be produced in various colors.
We've chosen about 10 colors to try out (so the prototype buyers will get one of their favorite case colors as well!) and then it's time to choose the mass production colors... then we're done here.
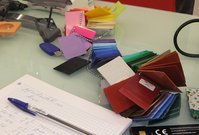
We've also decided on the plastic we'll use.
The base plastic is transparent, but by adding pulverized color, it will be completely opaque in that color.
The material is very flexible and durable. If you bend it, it doesn't break but immediately move back into it's original position.
According to the manufacturer, it is bulletproof (though I will NOT suggest you test that...)
I've captured a bit of the durability test using my camera... though I missed the best part: someone jumping on that plastic part, and the small hook you can see on the case didn't break.
Should be good enough for the battery lid, eh?
BTW: A quick physical test of the ugly-produced base part was successful.
I could put in the mainboard, insert a battery (and got some LEDs light up, so it works) and opening / closing the simcard as well as the MicroSD-card slot worked as well.
Here is the small video, first showing a bit of the production of the keyboard mold as well as the durability test of the plastic we've chosen.
Phewww, what a day.
I am sure you can imagine how shocked I was at the beginning, learning that I won't have a full set to assemble here, and the one part I've seen was ugly... but learning about all that above was interesting.
And it was really a good thing I came here, to decide about the material surface, the plastic and the color!
I hope you enjoyed the newspost, even though it was looooong and too much to read, probably
Well, here are some more pictures showing molds and tools.
You can also download them as 3D MPO files, if you got something to look at them in real 3D
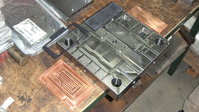
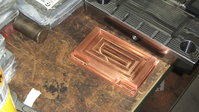
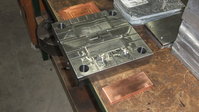
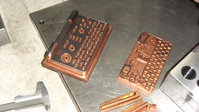
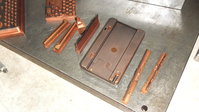
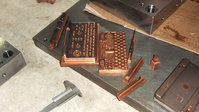
Attachments
-
DSCF2104.JPG3.3 MB · Views: 1,788
-
DSCF2105.JPG3.3 MB · Views: 1,833
-
DSCF2107.JPG3.4 MB · Views: 1,786
-
DSCF2108.JPG3.4 MB · Views: 1,775
-
DSCF2109.JPG3.3 MB · Views: 1,736
-
DSCF2110.JPG3.4 MB · Views: 1,735
-
DSCF2111.JPG3.3 MB · Views: 1,739
-
DSCF2112.JPG3.4 MB · Views: 1,700
-
DSCF2113.JPG3.3 MB · Views: 1,709
-
DSCF2115.JPG3.3 MB · Views: 1,690
-
DSCF2116.JPG3.4 MB · Views: 1,669
-
DSCF2117.JPG3.4 MB · Views: 1,687
-
DSCF2123.JPG3.4 MB · Views: 1,666
-
DSCF2124.JPG3.3 MB · Views: 1,663
-
DSCF2104.JPG3.3 MB · Views: 1,636
-
DSCF2105.JPG3.3 MB · Views: 1,641
-
DSCF2107.JPG3.4 MB · Views: 1,598
-
DSCF2108.JPG3.4 MB · Views: 1,562
-
DSCF2109.JPG3.3 MB · Views: 1,537
-
DSCF2110.JPG3.4 MB · Views: 1,526
-
DSCF2111.JPG3.3 MB · Views: 4,395
-
Photos3D.zip74 MB · Views: 635
Last edited: